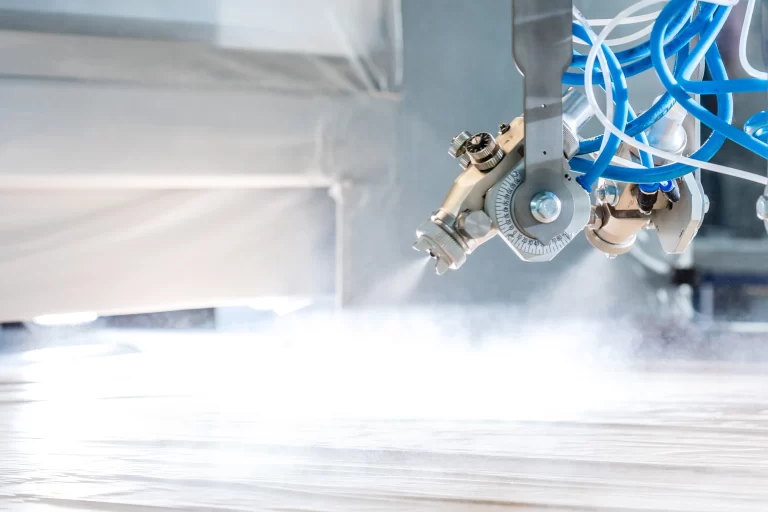
Good maintenance prevents downtime and frustration
In an environment where quality, timing and efficiency are key, reliable equipment is essential. Spray equipment, mixing systems and pump technology that run at full power every day have a hard time. Think processing different types of coatings, intensive use, and sometimes long downtimes between jobs. All these factors put a strain on your equipment.
Without regular maintenance, pipes, pumps and guns can become internally fouled. Wear on parts often goes unnoticed until it is too late: a sudden blockage, loss of pressure or leakage then causes unforeseen downtime. And just then you have no time to replace parts - if you have them in stock at all.
By opting for a preventive and periodic maintenance approach, you avoid that kind of scenario.
Preventive maintenance tailored to your working rhythm
Every production process is different. That is why we tailor our maintenance planning to your way of working: how frequently you use the equipment, what materials you work with, and what requirements there are around safety & timing.
During preventive maintenance:
-
the equipment is carefully dismantled
-
all components are thoroughly cleaned using a non-destructive method
-
we proactively replace critical wear parts
-
everything is reassembled and pressure-tested
That way, you can be sure that everything works optimally when you need it.
Problems do not usually arise suddenly, but are the result of accumulation, wear or small faults that accumulate. These are the most common defects we encounter in practice:
Blockage
-
Poor or incorrect rinsing after use
-
Incompatible paints processed interchangeably
-
Filters not cleaned or replaced on time
Blockages cause irregular spray images, loss of pressure or even complete stoppages.
Pumps
Piston pumps:
-
Leakage at upper seals
-
Poor sealing of balls, resulting in pressure loss or no pressure build-up
Diaphragm pumps:
-
Ruptured diaphragms due to dried-up material, long downtime or normal wear and tear
-
Valves not sealing properly or sticking, interrupting operation
Spray guns
-
Poor or asymmetric spray pattern due to contamination or distortion of the spray tip, air cap or needle
-
Leaks at the nozzle or trigger mechanism caused by wear or damage

Reliability starts with proper maintenance.
Maintenance is not an afterthought. It is an investment in reliability, continuity and peace of mind. By intervening in time, you avoid loss of production, expensive repairs or safety risks. Your equipment performs better, lasts longer and continues to meet your customers' quality requirements.
👉 Want to know what a customised maintenance plan for your installation entails? We are happy to think with you.