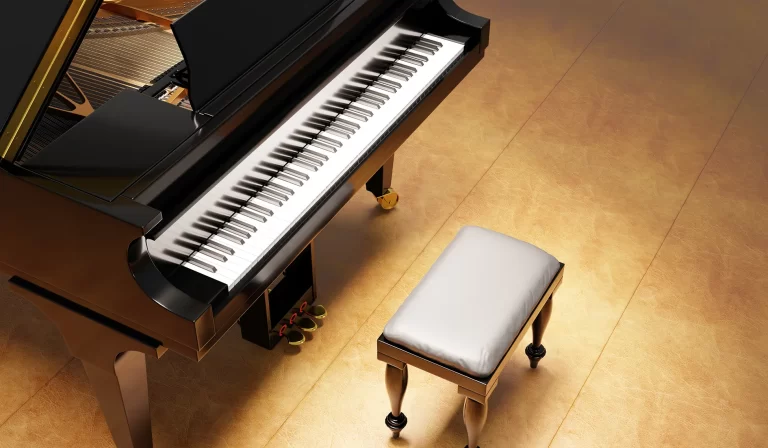
Low-pressure Nebulisation Technology: An Informative Overview
Several technologies exist within the low-pressure paint spray application segment, each offering specific advantages depending on the application. Choosing the right technology determines results, efficiency and production speed.
There are three main groups of low-pressure atomisation technologies commonly used in paint spraying applications:
- Conventional atomisation
- HVLP (High Volume, Low Pressure)
- Mid Pressure (RP, Trans-Tech, LVMP, LVLP, etc.)
Each of these technologies has specific characteristics suitable for different types of paint jobs. This article offers insight into the characteristics of these technologies, their benefits, and the areas of application, so that you can get a clear understanding of how each technique can best be used in different situations.
1) Conventional low-pressure atomisation
Conventional atomisation offers very fine atomisation and is ideal for applications where finish qualityof paramount importance. This system provides a superior finish and excellent control over paint deposition.
- Particle size: 7-8 µm
- Quality: Best finish quality
- Efficiency: Low, around 20-30%
Features:
- High finishing quality: Due to the fine atomisation smooth and detailed coatings applied. This makes it an excellent choice for paint jobs where the visual aspect is most important.
- Low efficiency: This system has a lower efficiency, which means more paint is consumed and the application is slower. This makes it less suitable for mass production.
Applications: Conventional nebulisation is mainly used for unique, high-quality products, such as design objects, where finishing quality is paramount.
2) HVLP (High Volume, Low Pressure)
HVLP is a popular atomisation technology known for its high return and reasonably good finish quality. It uses high air volumes in combination with low pressure, resulting in efficient and relatively fast application of paint.
- Particle size: 13-15 µm
- Quality: Coarser atomisation
- Efficiency: High, 45-65%
Features:
- Higher efficiency: With a return of 45-65% HVLP is much more efficient than conventional atomisation, so less paint is lost and the process is less costly.
- Reduced overspray: The low pressure provides less overspray and paint loss, making it an efficient choice for spraying larger areas.
- Coarser finish: HVLP does not offer the same fine finish as conventional technology, but it still delivers a high-quality coating, although in less detail.
Applications: HVLP is suitable for large areas where speed and return are more important than an extremely detailed finish, such as when spraying furniture or less detailed objects.
3) Mid Pressure (RP, Trans-Tech, LVMP, etc.)
The mid-pressure technology offers a optimum balance between paint finish and efficiency. This system combines the fine atomisation of conventional systems with the efficiency of HVLP technology, making it suitable for a wide range of applications.
- Particle size: 9-12 µm
- Quality: Fine atomisation
- Efficiency: High, 45-65%
Features:
- Excellent finishing: The fine atomisation delivers a very even coating and a nicer finish than HVLP.
- High efficiency: The efficiency of 45-65% makes mid-pressure technology both cost- and time-efficient, making it suitable for a wide range of applications.
- Flexibility: Mid-pressure is a versatile option suitable for applications where both finishing quality as productivity of interest.
Applications: The mid-pressure technology is widely used in mass production, automotive industry, and furniture production, where both speed as a finishing quality desired.
Choosing the Right Technology
The choice of low-pressure atomisation technology depends entirely on the nature of the project and the desired outcome. Here are some guidelines:
- For high-quality finishing and design products: Conventional atomisation is ideal if the finish quality highest priority.
- For large productions and high efficiency: HVLP or mid-pressure technologies offer excellent returnand fast application, with an acceptable finish for mass-market products.
- For a balance between finishing and productivity: Mid-pressure offers the best combination of paint qualityand return, suitable for applications where both speed and finish are important.

Each low-pressure atomisation technology has its specific advantages and disadvantages depending on the type of project. Whether you are aiming for superior finish quality for unique products or efficient application for mass production, it is important to choose the right technology that fits the goals and requirements of your paint application. By understanding how each technology works, you can make an informed choice that optimises your productivity without compromising on the final paint results.