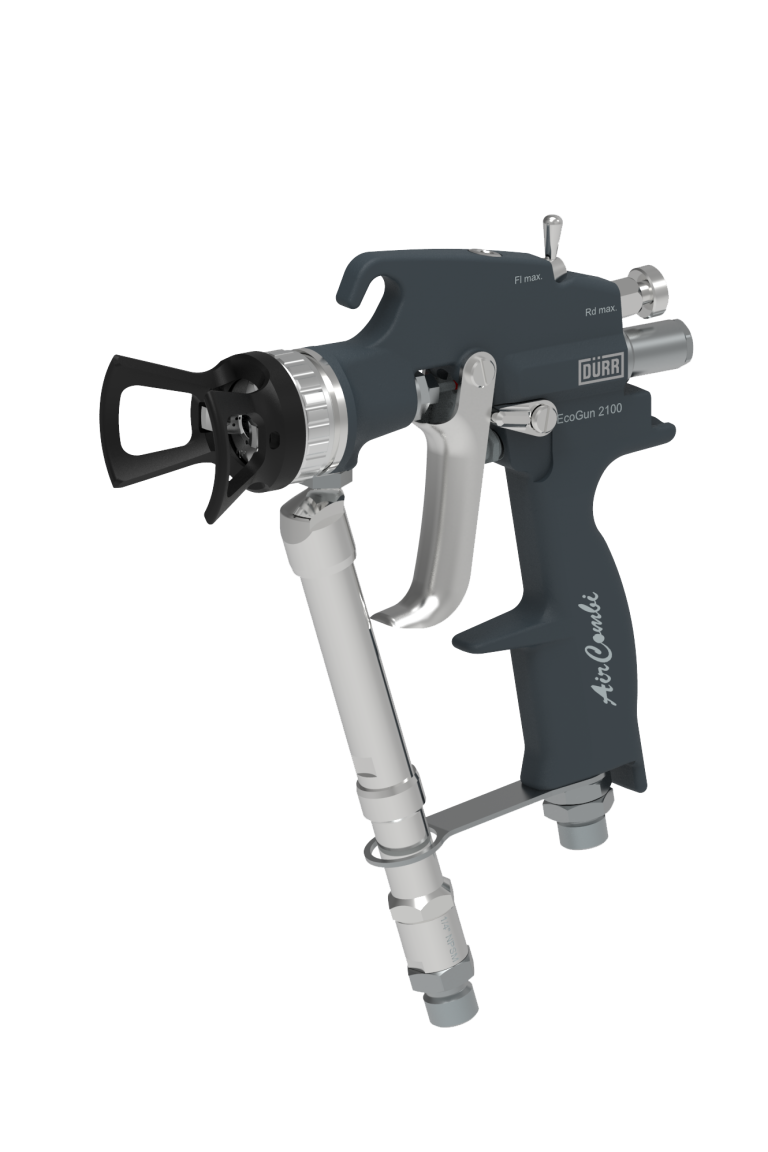
High-pressure atomisation: the power of Airless and Air Assisted Airless spraying techniques
The paint and coatings industry is all about precision and efficiency. One of the most widely used techniques for applying paint quickly and evenly is high-pressure atomisation, also known as Airless and Air Assisted Airless spray applications. This technology allows paint and other liquids to be sprayed with high pressure and precision, ensuring good, fast and effective results, when treating large areas or thick layers of paint.
In this article, we explain how this application method works, why it is so effective, and for which applications it is best suited.
What is high-pressure atomisation?
High-pressure atomisation works on the principle of all or nothing. This means that as soon as the trigger of the spray gun is pressed, the full flow of paint or liquid is released immediately, depending on the choice of nozzle or spray tip. This results in fast and efficient application of the paint, without any delay.
Airless spraying means that the paint is applied under high pressure - between the 50 and 500 bar - by the nozzle or spray tip is pressed, which has an opening between the 0.007" and 0.031" (0.18 to 0.79 mm). This small opening is crucial in determining the flow rate and the way the paint sprays. The design of the nozzle or spray tip determines the shape of the jet and the jet width.
How does the Airless spraying technique work?
The process is relatively simple: the paint or coating is fed to the spray gun via a pump. The pump puts the paint under high pressure and pushes it through the nozzle, where it is then dispersed and atomised. The result is a jet of paint that is forcefully sprayed onto the surface.
Air Assisted Airless spraying techniques add an additional airflow, which helps further optimise the spray jet. This ensures a smoother application and can help achieve an even coat.
Why use Airless and Air Assisted Airless Spraying?
Airless spray technology offers numerous advantages, especially for professionals who work with larger objects or surfaces, need to achieve high film thicknesses and process thixotropic paints. Here are some key reasons why this technology is popular in the paint and coatings industry:
-
Speed and efficiency: Due to the high pressure, a considerable amount of paint is applied at once. This saves time and increases productivity, especially on large surfaces such as steel structures or concrete.
-
Greater layer thicknesses: The technology is ideal for applying thicker layers of paint, such as primers or protective coatings, which are often more difficult to apply using traditional spraying techniques.
-
Even Distribution: Thanks to the high pressure and customised nozzle, the paint is evenly distributed over the surface, ensuring consistent coverage and a professional finish.
-
Powerful Application on Large Surfaces: Airless spraying is particularly effective for varnishing large objects, such as metal structures or machinery, where speed and quality are of paramount importance.
-
Cost-saving: Because the application method is fast and efficient, companies can do more work in less time, resulting in cost savings and higher profitability.
Applications of High-pressure atomisation
Airless and Air Assisted Airless sprayers are often used in the following applications:
-
Painting large objects: Think about steel structures, construction projects, or heavy equipment that need a consistent and durable coat of paint.
-
Application of primers and coatings: The ability to apply thicker layers of paint makes these techniques ideal for applying primers, which are essential for adhesion and protection of the underlying material.
-
Finishing Objects: Painting both industrial and commercial objects is simplified by the speed and evenness of application.
Basics of Spray painting
With high-pressure atomisation, it comes not only down to technique, but also to choosing the right equipment and the right type of paint. The choice of nozzle or spray tip, type of spray gun and paint pressure all affect the final result. Important considerations include:
-
Paint viscosity: The thickness of the paint affects how well it can flow through the nozzle or spray tip.
-
Nozzle or spray tip: The opening of the nozzle or spray tip determines the flow rate and the angle gives a specific spray width of the paint.
-
Paint spraying equipment: Airless and Air Assisted Airless systems have different characteristics and require specific maintenance procedures for optimal performance.
Conclusion
High-pressure atomisation, or Airless and Air Assisted Airless spraying, offers significant advantages for paint professionals working with larger objects or thick layers of paint. The technique offers speed, efficiency and even application, ensuring a high-quality finish for both industrial and commercial projects.

Are you looking for advice on the right spraying technique for your project or want to know more about the right equipment for Airless spraying? Then contact us for professional advice and the best products to take your work to the next level!